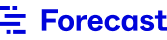
Achieving operational excellence is a strategic imperative for organizations seeking to gain a competitive edge in today's fast-paced and ever-changing business landscape. Operational excellence involves optimizing processes, reducing waste, and continuously improving to deliver high-quality products or services efficiently and consistently.
By following a structured roadmap, businesses can navigate this journey more effectively and reap the rewards of operational excellence, including increased profitability, enhanced customer satisfaction, and a stronger market position.
The first step in building operational excellence is to define your vision and goals clearly. This involves establishing a shared understanding of what operational excellence means for your organization and aligning it with your overall business strategy.
Begin by engaging key stakeholders, such as executives, managers, and frontline employees, in a collaborative process to define your vision for operational excellence. This vision should be aspirational yet achievable, and it should resonate with the values and culture of your organization.
Once you have established your vision, identify specific, measurable, achievable, relevant, and time-bound (SMART) goals that will guide your operational excellence initiatives. These goals could include reducing costs by a certain percentage, improving quality metrics, increasing customer satisfaction scores, or enhancing productivity levels.
Clearly communicate your vision and goals to everyone involved, as this will serve as the foundation for your operational excellence initiatives and help ensure alignment and buy-in across the organization.
With your vision and goals defined, the next step is to conduct a comprehensive assessment of your organization's current state. This involves analyzing your processes, systems, and performance metrics to identify areas of strength and weakness, bottlenecks, inefficiencies, and opportunities for improvement.
Utilize a variety of tools and techniques to gain a deep understanding of your current operations. Process mapping can help visualize and analyze your end-to-end processes, revealing potential areas for improvement. Value stream mapping can identify waste and non-value-added activities within your processes. Data analysis can provide insights into performance metrics, trends, and areas for optimization.
Engage employees at all levels during this assessment phase, as they often have valuable insights into the challenges and inefficiencies they face daily. Conduct interviews, surveys, and focus groups to gather their perspectives and feedback.
Based on your assessment, develop and implement strategies to address the identified areas for improvement. This may involve process redesign, technology upgrades, employee training, or cultural shifts.
Lean methodologies, such as Lean Six Sigma, can provide a structured approach to identifying and eliminating waste, streamlining processes, and improving quality. Lean Six Sigma combines the principles of Lean manufacturing, which focuses on reducing waste and increasing efficiency, with Six Sigma's data-driven approach to identifying and eliminating defects and variability.
Continuous improvement frameworks, like Kaizen, can foster a culture of ongoing learning and incremental improvements. Kaizen encourages employees to identify and implement small, incremental changes that can lead to significant improvements over time.
Encourage employee involvement and empowerment throughout this process. Frontline employees often have valuable insights and ideas for improving the processes they work with daily. Implement mechanisms for capturing and evaluating employee suggestions, and provide recognition and rewards for successful improvements.
Operational excellence is not a one-time effort but an ongoing journey of continuous improvement. Continuously monitor your performance metrics and gather feedback from customers, employees, and other stakeholders. Use this information to identify new areas for improvement and adjust your strategies accordingly.
Establish a system for regularly reviewing and updating your processes, technologies, and improvement initiatives. This could involve periodic process audits, performance reviews, or dedicated continuous improvement teams responsible for identifying and implementing improvements.
Celebrate successes and learn from setbacks, as they can provide valuable lessons for future improvements. Foster a culture of learning and continuous improvement by encouraging open communication, knowledge sharing, and a willingness to experiment and take calculated risks.
Building operational excellence is a challenging but rewarding journey that requires commitment, perseverance, and a willingness to continuously improve. By following this 4-step roadmap, organizations can navigate the path to operational excellence more effectively, delivering high-quality products or services efficiently and consistently while fostering a culture of continuous improvement. The result is a more competitive, agile, and sustainable organization that can adapt to changing market conditions and customer needs.
The ultimate upgrade to delivering projects on time and on budget.
Request a Demo